Pipeline Welding Inspection: Guarding Pipelines with Precision and Knowledge
Pipeline Welding Inspection: Guarding Pipelines with Precision and Knowledge
Blog Article
Understanding the Fundamentals of Pipe Welding Evaluation: Important Variables for Examining Weld High Quality and Averting Failures
In the world of pipe welding evaluation, the risks are without a doubt high, requiring a complete understanding of essential principles to guarantee weld top quality and minimize failing threats. Various crucial aspects enter play, including the selection of ideal products, the application of innovative examination strategies, and the acknowledgment of widespread welding flaws. Furthermore, adherence to regulatory requirements plays a crucial role in preserving system honesty. Yet, the complexities intrinsic in these procedures elevate vital inquiries concerning ideal practices and arising modern technologies that can redefine assessment protocols-- questions that necessitate further exploration.
Value of Weld Quality
The honesty of a pipeline is fundamentally reliant on the high quality of its welds, making weld quality a vital consider ensuring safe and effective procedure. A pipe weld works as a junction point where products are joined, and any deficiencies around can lead to considerable architectural weaknesses. Poor bonded quality can cause leakages, ruptures, and devastating failings, posing major safety risks and ecological dangers.
Numerous elements add to the high quality of a weld, including the choice of welding process, the abilities of the welder, and the problems under which the welding is performed - Pipeline Welding Inspection. Insufficient prep work, inappropriate warmth input, and contamination can jeopardize weld honesty, bring about problems such as porosity, insufficient combination, or fractures. Consequently, rigid quality control procedures need to be applied throughout the welding process to alleviate these risks
In addition, the lasting efficiency of a pipe is greatly influenced by the resilience of its welds. Premium welds not only boost the overall toughness of the pipeline but additionally prolong its solution life, minimizing the need for pricey repairs and downtime. For this reason, making certain remarkable weld top quality is paramount in pipe layout and upkeep practices.
Key Inspection Techniques
Making sure weld top quality requires the execution of reliable assessment techniques to determine potential defects before they lead to failings. Pipeline Welding Inspection. Amongst the most widely utilized approaches are aesthetic inspection, radiographic screening (RT), ultrasonic testing (UT), and magnetic bit screening (MT) Each technique is and serves an unique purpose chosen based upon the specific requirements of the pipe job
Visual inspection is the very first line of defense, enabling assessors to analyze surface conditions, positioning, and overall workmanship. It is a cost-effective and quick method that can expose evident defects. Radiographic screening supplies a thorough sight of internal weld integrity by utilizing X-rays or gamma rays to find subsurface problems. This strategy is particularly reliable for identifying cracks, additions, and gaps.
Ultrasonic screening utilizes high-frequency audio waves to assess the thickness and stability of welds, making it optimal for finding inner stoppages. Magnetic fragment testing is a reliable method for identifying surface area and near-surface issues on ferromagnetic materials by applying electromagnetic fields and fine ferrous particles. By utilizing these vital assessment methods, pipe welding examiners can ensure the finest quality criteria are preserved, ultimately resulting in more secure and extra reliable pipe systems.
Usual Welding Flaws
In the world of pipeline welding, recognizing usual welding defects is vital for preserving architectural honesty and safety. These flaws can bring about devastating failures if not recognized and addressed quickly. Among one of the most common issues are porosity, which occurs when gas entraps in the weld metal, producing voids that compromise the joint. Another significant issue is absence of combination, where the weld steel does not adequately bond with the base product, jeopardizing the joint's strength.

Splits are additionally an essential problem, showing up in different kinds such as hot splits, cold splits, and root splits. Each type postures one-of-a-kind obstacles and calls for certain assessment techniques for discovery. Undercut is another defect that can decrease the weld's cross-sectional area, leading to stress and anxiety concentration factors, while slag inclusion happens when non-metallic material ends up being caught in the weld pool, adversely affecting the mechanical residential properties of the weld.
Furthermore, inaccurate bead form can result in unequal stress circulation. Recognizing these usual defects is vital for welders and inspectors alike, as early discovery and modification are important to guaranteeing the durability and integrity of pipeline systems.
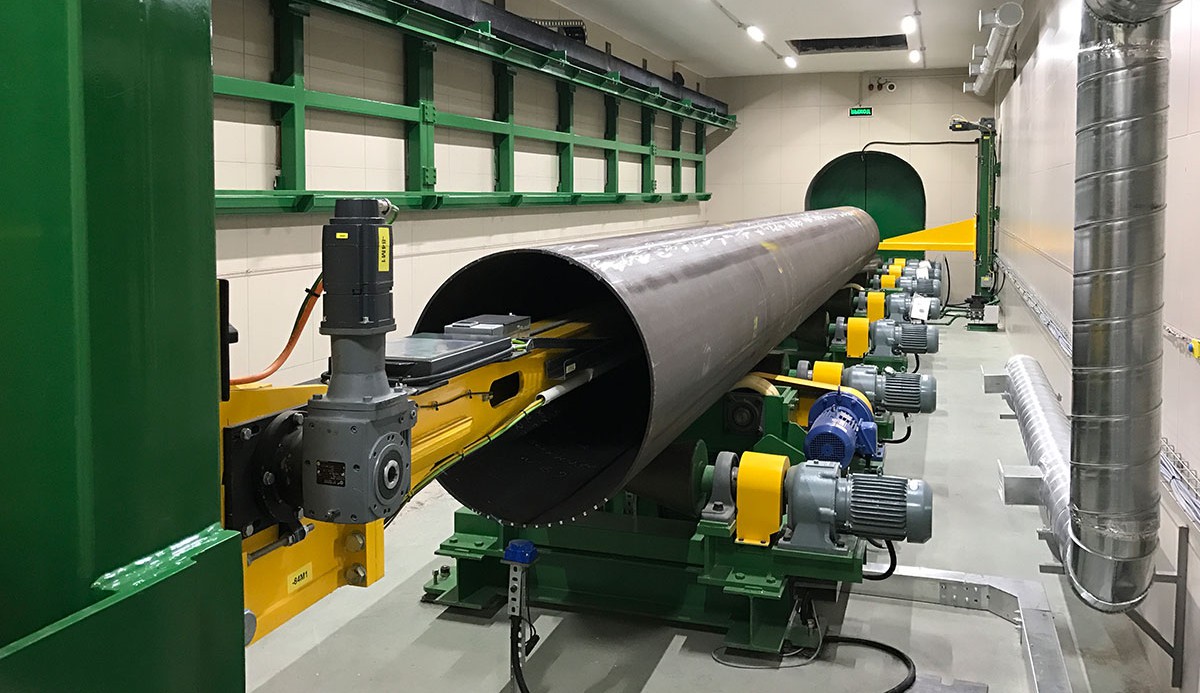
Materials and Their Impact
Choosing the suitable products for pipe welding dramatically affects the general efficiency and dependability of the welded joints. The selection of base steels, filler materials, and layers plays a critical function in determining the stamina, corrosion resistance, and sturdiness of the welds. For circumstances, carbon steel is generally utilized for its balance of strength and expense, yet it may be prone to corrosion in particular environments, necessitating making use of protective layers or corrosion-resistant alloys.
Additionally, different steel welding requires careful factor to consider of thermal development buildings and possible galvanic rust. The compatibility of products can considerably impact the microstructure of the weld, resulting in variants in mechanical residential or commercial properties. For instance, stainless steel supplies superb corrosion resistance yet might need details filler materials to guarantee an audio weld joint.
Furthermore, the effect of temperature level and environmental conditions on product choice can not be underestimated. High-strength steels might shed ductility at raised temperatures, while low-temperature applications might need pop over to these guys materials with enhanced sturdiness. Ultimately, recognizing the implications of product selections is important for achieving optimum weld high quality and avoiding failings in pipeline systems.
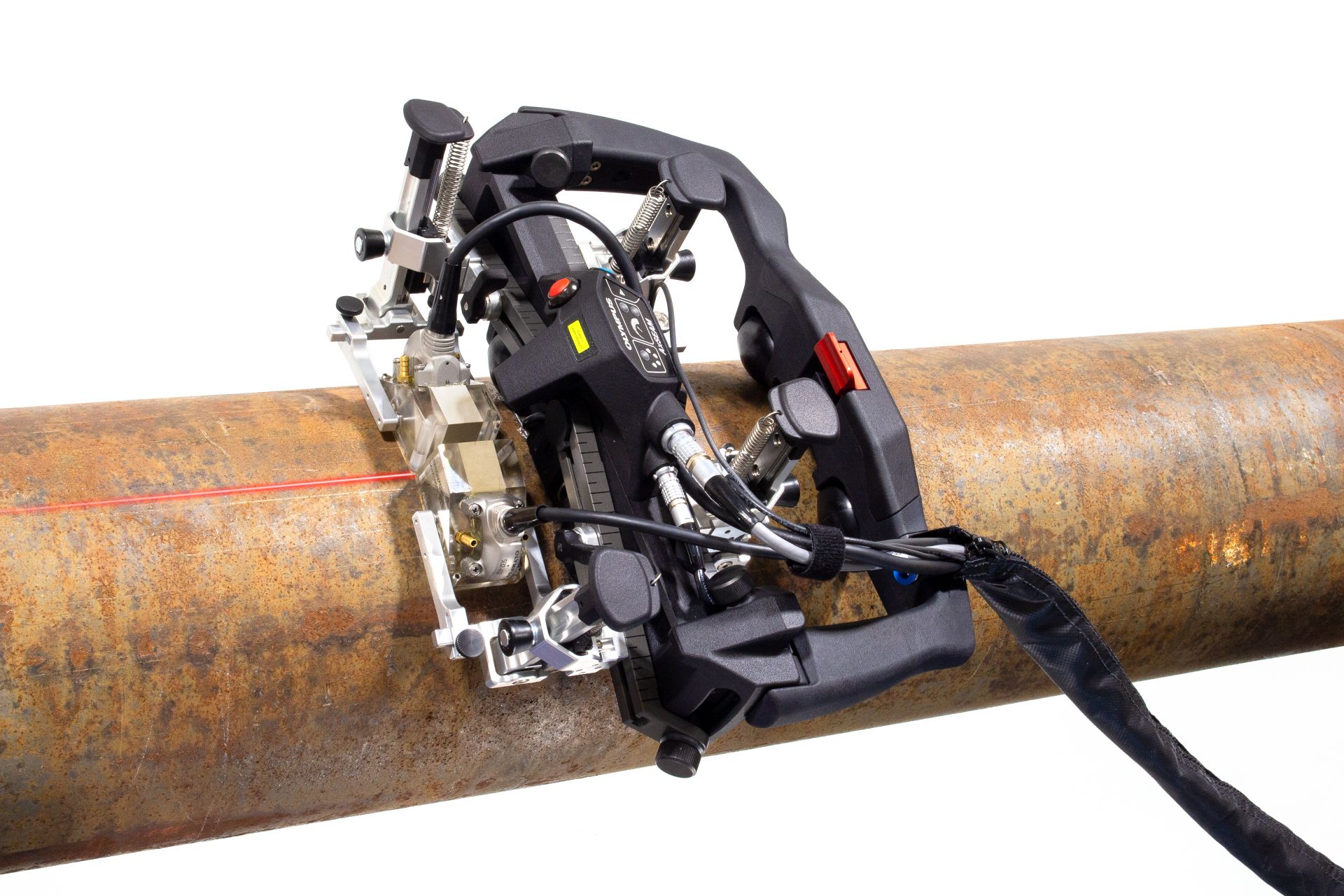
Regulatory Requirements and Conformity
Regulative criteria and conformity play a pivotal function in pipeline welding, developing the structure within which risk-free and effective practices are maintained. These standards are developed by numerous organizations, including the American Society of Mechanical Engineers (ASME), the American Welding Culture (AWS), and the Pipe and Hazardous Materials Security Administration (PHMSA) Abiding by these regulations guarantees that welding treatments satisfy the required high quality and security criteria.
Compliance with regulatory criteria is important not just for making certain the honesty have a peek at these guys of the welds but additionally for safeguarding the atmosphere and public security. Assessors are entrusted with confirming that welding operations follow these criteria via extensive exams of both the processes and the last welds. This entails evaluating welder credentials, welding treatments, and the products used.
Failure to abide by well established policies can bring about substantial consequences, consisting of pricey repairs, lawful liabilities, and disastrous failings. Therefore, companies have to integrate conformity right into their functional techniques, cultivating a society of safety and quality. Normal training and audits are crucial parts in keeping adherence to these regulatory criteria, making sure that all personnel are well-informed and outfitted to support the highest degrees of pipeline welding quality.
Conclusion
Finally, an extensive understanding of pipe welding evaluation is crucial for guaranteeing weld high quality and stopping failings. By using vital examination techniques and acknowledging common welding flaws, assessors can properly assess the honesty of welds. Factor to consider of product option and adherence to governing criteria better boost the reliability and safety and security of pipeline systems. Inevitably, these methods add to the prevention of leakages and tragic failures, underscoring the vital relevance of extensive assessment processes in pipe building and construction and upkeep.
In the world of pipeline welding examination, the stakes are undeniably high, demanding an extensive understanding of basic principles to make certain weld high quality and reduce failure threats (Pipeline Welding Inspection).The honesty of a pipeline is basically reliant on the high quality of its welds, making weld high quality a critical aspect in making certain safe and effective procedure.Several aspects add to the find quality of a weld, including the selection of welding procedure, the abilities of the welder, and the conditions under which the welding is done. Undercut is an additional problem that can decrease the weld's cross-sectional location, leading to tension concentration factors, while slag inclusion takes place when non-metallic material becomes caught in the weld pool, adversely affecting the mechanical residential or commercial properties of the weld
In final thought, a detailed understanding of pipeline welding examination is crucial for making certain weld high quality and protecting against failings.
Report this page